Pressure Transmitters
&
Differential Pressure Transmitters
Pressure transmitters are devices used to measure pressure and convert it into an electrical signal, typically a 4-20 mA current loop or digital output. These transmitters are widely used in various industries for process monitoring, control, and automation. Here are some common types of pressure transmitters:
1. Absolute Pressure Transmitter: Measures the pressure relative to a perfect vacuum (absolute zero pressure). These transmitters are used in applications where pressure readings need to be referenced to absolute zero.
2. Gauge Pressure Transmitter: Measures the pressure relative to atmospheric pressure (the gauge pressure). They are commonly used for most industrial applications, as they provide pressure readings in reference to the surrounding atmospheric pressure.
3. Differential Pressure Transmitter: Measures the difference in pressure between two points in a system. They are used for applications such as flow measurement, filter monitoring, and level applications.
4. Sealed Pressure Transmitter: This type is designed to measure pressure without being influenced by changes in atmospheric pressure. It is sealed to prevent the entry of outside air.
5. Vacuum Pressure Transmitter: Measures pressures below atmospheric pressure (negative pressure or vacuum).
6. High-Pressure Transmitter: These transmitters are specifically designed to measure very high pressures, often used in heavy industries or applications requiring high-pressure measurements.
7. Low-Pressure Transmitter: Suitable for measuring low-pressure ranges, typically used in applications like HVAC systems and medical devices.
8. Compound Pressure Transmitter: Measures both positive and negative pressures, suitable for applications with pressure variations in both directions.
Pressure transmitters are versatile devices, and their selection depends on the specific application, pressure range, accuracy requirements, environmental conditions, and compatibility with the control or monitoring system. They are essential tools for maintaining efficient and safe operations in many industrial processes.
Differential pressure transmitters are devices used to measure the difference in pressure between two points in a system. They are commonly used in various applications where monitoring and controlling pressure differences are critical. Here are some common types of differential pressure transmitters:
1. Diaphragm Differential Pressure Transmitter: This type uses two diaphragms that are exposed to different pressures. The difference in pressure between the two diaphragms causes deflection, which is then converted into an electrical signal proportional to the differential pressure.
2. Capacitive Differential Pressure Transmitter: Capacitive differential pressure transmitters measure the change in capacitance between two plates that are exposed to the differential pressure. The change in capacitance corresponds to the difference in pressure and is converted into an electrical signal.
3. Strain Gauge Differential Pressure Transmitter: In this type, strain gauge technology is used to measure the strain changes in response to the differential pressure. The strain gauges are placed on a flexible diaphragm or element, and the resulting deformation provides an output signal.
4. Piston Differential Pressure Transmitter: These transmitters use a piston that moves in response to the pressure difference. The movement of the piston generates an output signal proportional to the differential pressure.
5. Bellows Differential Pressure Transmitter: Bellows-type differential pressure transmitters use a flexible metal bellows that expand or contract with the pressure difference. The movement of the bellows generates an electrical signal representing the differential pressure.
6. Variable Area Differential Pressure Transmitter: Also known as a “flow meter with a differential pressure transmitter,” this type is used to measure flow rates by detecting the pressure difference across an orifice or a restriction in a pipe.
7. Smart Differential Pressure Transmitter: This type includes advanced features such as digital communication protocols (HART, Modbus, Foundation Fieldbus, etc.), self-diagnostic capabilities, and remote configuration options.
The selection of a differential pressure transmitter depends on the specific application, the range of pressure differences to be measured, accuracy requirements, environmental conditions, and compatibility with the control or monitoring system. These transmitters play a crucial role in various industries, including process control, HVAC systems, petrochemicals, pharmaceuticals, and many others.
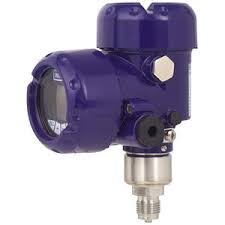